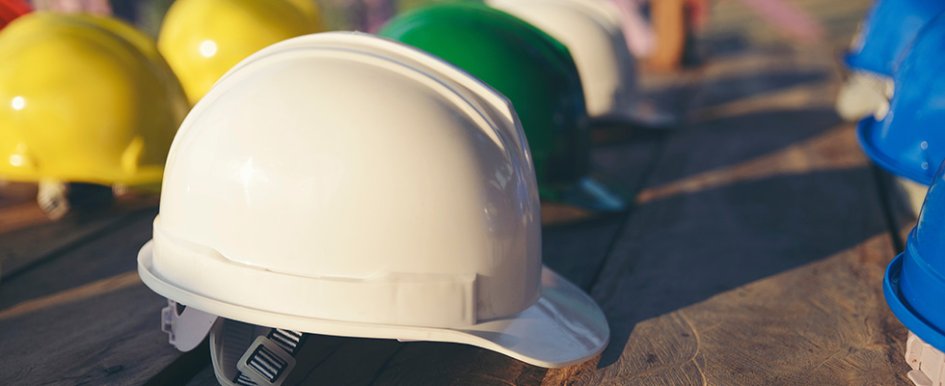
While we typically think of an experience modification rate (EMR) as a data-driven calculation used to determine an insurance premium for construction companies, it takes a very high-touch, personal approach to successfully keep that score low. A lower EMR results in tangible business-related benefits, including cost savings, competitive bidding advantages, fewer workers’ compensation or negligence cases and improved financial stability. But behind those quantitative business results must be a strong culture of safety with a straightforward goal: Come to work to support your family, but get home safely to them too. With that goal in mind, a strong safety-first culture contributes to overall employee morale, attracts top talent and improves worker productivity. While eliminating jobsite injuries is virtually impossible, many strategies can be implemented to establish a culture of safety and help lower your EMR.
Building a Safety-First Culture
At the core of all successful safety programs is a commitment from the company leadership. That commitment starts with leadership taking an active, on-site role rather than solely monitoring safety processes from an office somewhere. The most effective leaders are on the jobsites and leading a safety department that is not structured to police compliance but to build relationships with field employees, customers, vendors and others.
With subcontractors, safety expectations are established even before they set foot on the jobsite. Pre-qualifying subcontractors ensure they have proper insurance, written procedures and EMRs below the industry standard. Spell out specific safety policies in trade partner contracts, as proactively outlining expectations upfront ensures the most competent workers are joining your team.
Communication and documentation are essential. Not only do they ensure an understanding of procedures upfront, but documentation can be a crucial resource for potential disputes or claims cases. It’s important to have workers review and sign off on individual orientation sheets confirming they’ve been debriefed on all hazards or potentially hazardous situations. Be sure to gather worker certifications and maintain them on-site to ensure that anyone operating equipment is certified to do so. Require individuals on a jobsite to sign “hold harmless” agreements at a company level and project site visitation agreements at the individual level.
Involve employees in safety committees and decision-making, and then recognize and reward employees for their contributions to workplace safety. Any site can keep an incident-free record when all trades work together and communicate.
Relationship Building
When creating a culture of safety, there needs to be a focus on relationship building. Team leaders must foster a culture of trust, accountability and responsiveness regarding safety, demonstrating that the entire company is working together as a united front. It’s essential to strive to be consistent in documentation and procedures so that every worker receives proper training and information regarding the present hazards. It’s also crucial to keep open lines of communication, allowing superintendents to get the support they need to safeguard their sites adequately.
When there’s a strong relationship in place, there’s no jobsite tension when the safety team conducts unscheduled inspections to verify that work is being undertaken to company and state standards. Superintendents should welcome input from the safety team to determine operations requiring a job hazard analysis or crane pick plan.
Ensure you leverage opportunities to reinforce your safety commitment through special events and communication. For example, your company could hold regular safety education events and use these events to plan, inspire, educate, and build relationships with all employees and field workers. When hosting events like this, consider bringing in sponsors from key manufacturing or service partners to demonstrate the newest safety features in their products and services. Hold stand-downs with industry and company leaders, but also hold stand-downs that are a little different, like a lunchtime yoga class or other wellness education. Training events are a great way to bring the entire team closer and remind each other of their shared safety goals.
Relationship building is just as important with all vendors and trade partners too. Having top-to-top meetings with these partners, in addition to the daily interactions with individuals on the jobsite, is essential to establishing expectations related to worker safety. Other benefits are earned when positive relationships are established with these partners, like referrals to other like-minded vendors and trade partners. Good subs always want to work alongside other good subs, further strengthening culture.
Make a Commitment to Training
A culture of safety isn’t an end goal but something to evolve and improve continually. A leadership team that recognizes this and commits to advancing safety protocols to protect all workers at every jobsite is integral to building a safety culture. Review and evaluate your training partners regularly to ensure your workers have the most accurate and industry-leading safety training. Is your training provider an authorized provider of continuing education credits? This is something to think about as you review your training resources. Implementing new technologies that proactively manage safety certifications and on-site training can help to keep safety documentation up to date and ensure that only properly certified workers are accessing a jobsite. Also, ensure your safety inspection process is constantly being updated and modified to ensure compliance with new standards, and that recurring hazards are discussed and checked with each visit. Consider requiring your superintendents and project managers to complete training protocols to educate and improve safety conditions. The more eyes on safety, the more hazards you can mitigate.
Measuring Success
A low EMR has an impact well beyond insurance rates. When you can show clients, potential new hires and the insurance company that you take safety seriously, you open the door to relationships with new customers who value work being completed safely. It also brings additional work from current customers who know you as a quality partner. Your company’s EMR can provide access to top talent proud to work for a company dedicated to getting the job done with safety at the forefront.
Holding a low EMR also keeps you well-informed and well-prepared for potential workers’ compensation or negligence disputes. Proper documentation, including clear incident reports, photos and witness statements, protects your company from fraudulent or inaccurate claims. Accurate reporting and regular claims review can contribute to quicker, fairer settlements.
Remember that reducing your EMR is a long-term effort requiring consistent safety and risk management dedication. It may take time to see significant improvements, but the benefits of a lower EMR can positively impact your business’s bottom line and employee well-being.